Today, it’s my pleasure to be able to ask all of my questions to two great brothers and friends of mine - Ralf and Roy from Ayasa instruments. I’m a handpan enthusiast and I wanted to know more about this new material they have developed in recent months. When I put one of their new instruments on my lap, I fell in love with the timbre of the shell, the sustain, the quality, stability and isolation of the notes ? As a complete geek, I wanted to know more about this new material. How is it different from other steels? How did they arrive at this point? What were they trying to do? How has this material changed the way they work? And more...
If you are as curious as me and if you’d like to grow in your knowledge about the handpan and its evolution, then this article and the Ember Steel Handpan is for you. 😀
Happy reading, and don’t miss my demo on one of their instruments at the end of this article.
Before we speak of Ember Steel, could you remind us of the differences between all the mainstream steel materials? We feel lost as players... (Nitrided, DC04, Stainless, etc)
Handpans are traditionally made with industrial sheet steel that is mostly used in the Automobile Industry. There is a classification ranging from DC01 to DC07 and out of those seven grades the most commonly used steel for making handpans is the middle grade: DC04.
One of the main disadvantages is that this steel is prone to rusting. By nitriding; heating and at the same time diffusing nitrogen into the material, it becomes harder and (partly) protects the material from rust. Nitrided DC04 instruments are, in general, known for their ceramic sound and relatively shorter sustain (i.e. the amount of time a note sings).
Although some handpan makers have been making stainless steel handpans for quite some time, only in the last few years did we see a real rise in popularity. Stainless steel of the type AISI 430 is known for its long sustain and has been the most used stainless steel for handpans in recent years.
When we laid our hands on our first deep drawn stainless steel shells we were sold! We switched our entire production of instruments from nitrided to stainless material immediately!
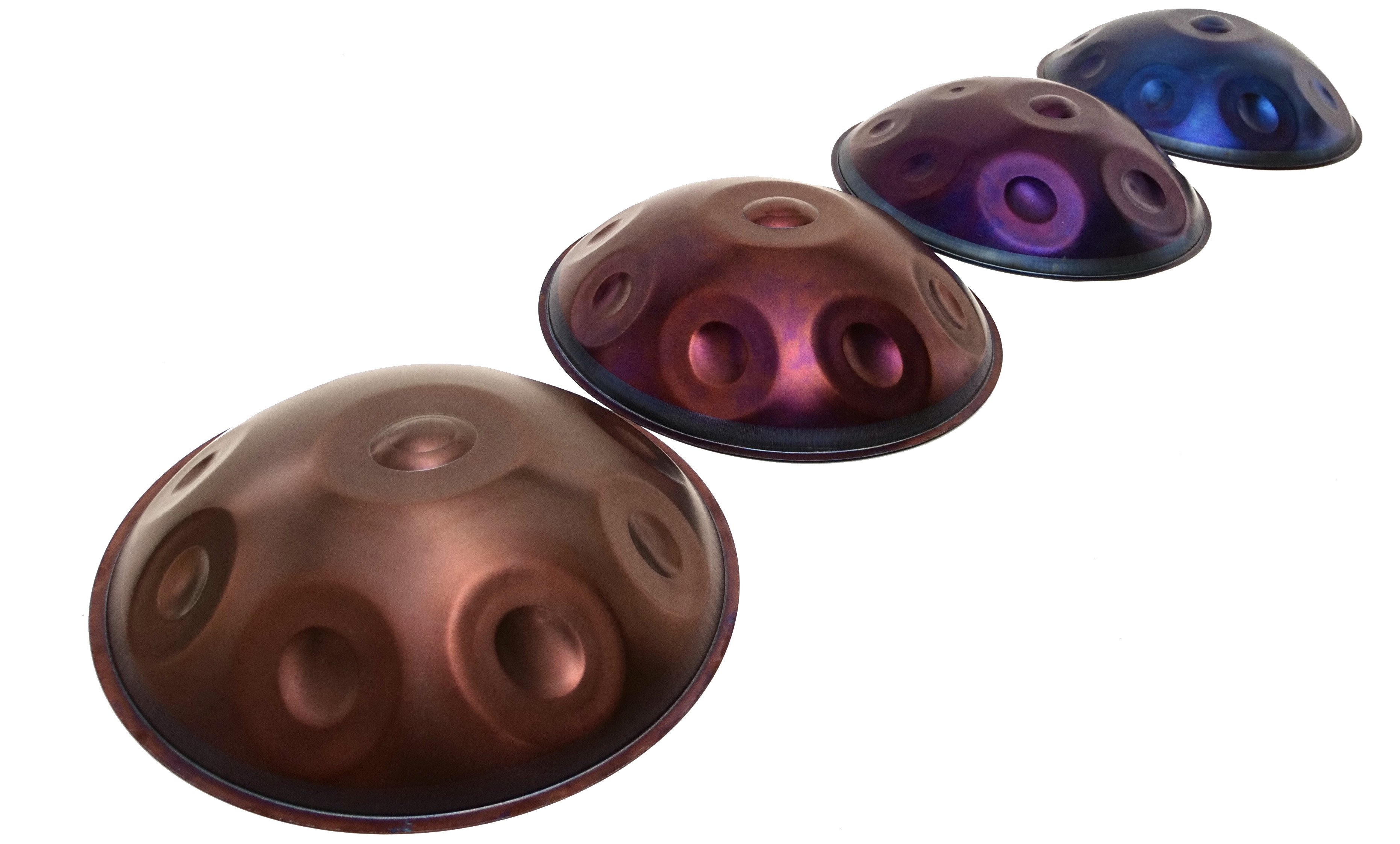
What is Ember Steel exactly ? Is it stainless?
Ember Steel is indeed a type of stainless steel. It differs from other types of stainless steels, such as AISI 430, in terms of its chemical composition and mechanical properties.
Since our discovery of this material in the summer of 2020 we have been only making Ember Steel handpans. We love working on, and of course playing, these Ember Steel instruments.
What kind of sound were you trying to render/get?
The qualities that we are looking for in a material are multiple:
- A long, controlled, sustain is paramount.
- It is important to have a good note isolation, so you do not get unwanted activations of surrounding notes (crosstalk).
- Furthermore we look for a sensitive and responsive touch and at the same time great stability so that you can not overblow the notes by striking hard. This quality is also linked to a high dynamic range; players get a very low volume sound when softly striking the notes and very loud volume when striking hard.
- Lastly we also look for a sound that is not too metallic and thin but rather ceramic and full.
Note: If all these concepts seems a little vague to you, take a look at this article: 7 marks of a quality handpan.
What brought you to this material?
The vision of sound that we just talked about is what drove us to search for a new material. We had been exploring the sound of nitrided steel for more than 6 years and we felt we were reaching a limit; the depth in playing that a longer sustain easily gives you was still missing. Therefore, we tested a wide variety of materials.
For instance, we had great results with a certain type of high carbon steel; which we called Iddha. When we ordered a big batch of this type of steel it turned out to be too hard to deep draw despite successful tests earlier. It also still had rust issues. It cost us a lot of time, effort and resources but we really learned a lot from the process!
Once we started working with deep drawn stainless AISI 430 and loved it, we knew we were going in the right direction.
We were welcomed into the infinite world of stainless steels! From thereon were a few different candidates with qualities we are looking for but they all had one or more downsides, we kept looking for a material that checked all our boxes. Finally we found what we now call Ember Steel.
How did you find the name?
When we heard our first instrument made with Ember steel we were pleasantly surprised by the warmth of the sound. Combined with the blend of the deep golden, orange, red and purple colors of the material, it reminded us of glowing embers in the campfire. Soon the name Ember Steel became our favorite!
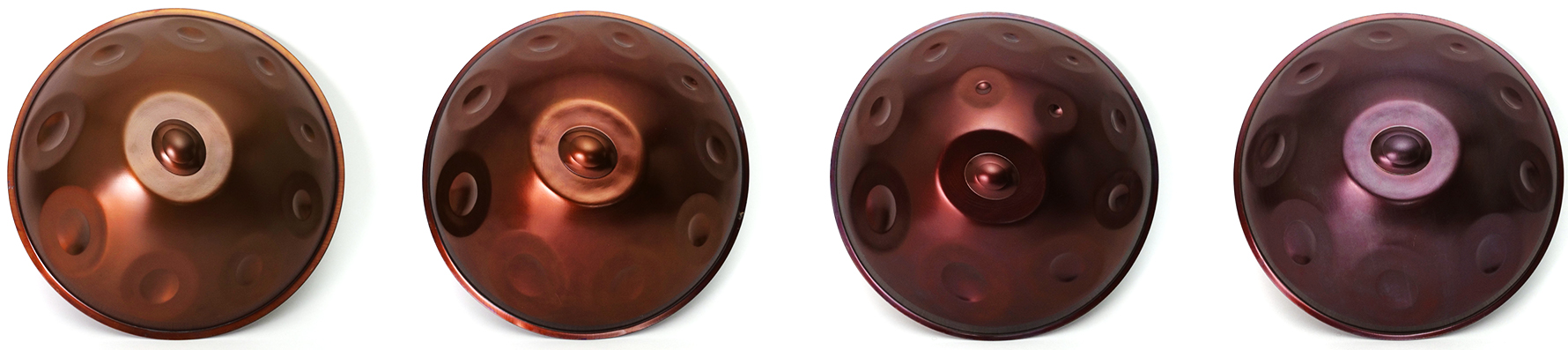
Is Ember Steel suitable for any playing style? What are the pros and cons of this material for the sound of the instrument?
Most handpan players directly fall in love with the sound of Ember Steel when they first play it. You can mostly play the same way you play any other handpan, however most people soon find out they can dive deeper into the sound in many ways.
With nitrided instruments you are often forced to play faster to avoid silence without you even realising it. With stainless materials, you can slow down because of the longer sustain filling the void. In our experience, Stainless AISI 430 can feel a little bit wild and tinny (less ceramic) and this of course also depends on the build quality of the instrument. With Ember Steel we noticed the longer sustain is there but more controlled, allowing you to play both slow and fast with ease.
Ember Steel is loved by professional artists, experienced players and also beginners players. We notice that when customers new to the handpan come to our workshop and try the different material handpans, it is easier for them to get a clear sound and more volume out of Ember Steel instruments compared to nitrided or regular stainless. This is mainly because of its sensitive and highly responsive touch. Thus with less skill and technique, the Ember Steel handpans seem a lot easier to start playing!
For a relative few however, the sustain of any stainless type steel is too long, and they feel that playing disharmonic notes in rapid succession creates an undesired sound. You can however experiment with muting notes swiftly after playing them in order to stop disharmony.
What are the pros and cons of this material for the instrument?
Practical advantages of this material are its increased rust protection and stability. Even stainless AISI430 can oxidize; even though it is only a superficial and mainly aesthetic. Ember Steel does not rust at all, therefore it will keep its nice surface finish with it’s beautiful colors that we get after heat treatment and you don’t have to worry about cleaning and oiling your instrument much at all. With a nitrided instrument you always need to be wary of any rust formation as it could eat through your instrument on the long run.
Ember Steel is also a very stable material if the instrument is constructed and tuned well. Meaning that the notes should not so easily go out of tune and will not break/overblow that easily while striking. So far we haven’t found any real downsides, other than that for most makers it takes a bit more time and effort to make an instrument from this material.
How does this material change the process making?
Material, to a certain degree, affects the optimal building process. It all starts with shaping; how deep you want to shape, the size of the tone fields, dimples etc. Once the instrument is shaped and going into the oven for annealing (in order to stabilize and harden the material) we figured out that the normal 400 degrees Celsius as for nitrided steel was not enough.
Ember Steel works best for us between 550 and 650 C! It’s very hot indeed. When you open the oven at this peak temperature the metal is glowing hot! Really like embers in the fire…
To tune any kind of stainless material stable, you will need to work with a greater attention to detail than when tuning nitrided steel. Ember Steel has been our greatest teacher in the last year, giving us much more feedback than any other material, teaching us to better balance tone fields and the instrument as a whole.
There are a lot of different tensions and aspects to consider but the key element is to balance all tensions in and around the membrane. We distinguish the two most important tensions from our experience. We don’t want to have much tension inside the membrane (internal tension), but primarily around the border of the tonefield (external tension).
You can think of a djembe drum skin to imagine what we mean. You raise the tension and thus the frequency of the drum by tightening the ropes on the edge of the skin, not somewhere inside the membrane. Internal tension creates a weaker sound and a less stable tuning. Besides, tuning all notes as free as possible from the internal tension will make them sound much more balanced all together.
By the way, if you're interested about the science behind handpans, checkout my article on How are handpans made and why they sound so amazing and unique.
Does making instruments with this material affect the price of your instruments?
No, even though it does indeed require more time and attention to detail to make instruments from Ember Steel, we kept the price level the same.
Our pricing is as follows:
- €2000 base price
- Plus €200 per note making
A nine note instrument including the center note cost €2000.
On our website you can see the models that we have available now and you can email us for a custom order. However, at the moment we are too busy to accept new custom orders and we do not have any Ember Steel instruments on the “available now section” because of the high demand. We hope to have some available soon!
Working with a long waiting list full of customer orders is very challenging and time consuming for us, any extended model goes through a series of tries to make sure we have the perfect balance between ease of playing, purest sound and least amount of unwanted crosstalk and activations.
Therefore, our focus now lies on perfecting the layouts of our favorite extended models:
- D Ashakiran 17
- E Amara 21
- C# Pygmy 17
- D Kurd 15
- C Aegean 17
and others so that we can raise their quality and offer these more frequently to our available now section.
Is this material available for other makers? Do you sell shells?
Yes! We can not possibly make enough Ember Steel handpans for everyone in the world and therefore we felt we needed to make these shells available for other makers so that more people can enjoy the soothing sounds of Ember Steel handpans. Makers can find more about Ember Steel on our website.
David :
Wow! Thanks guys for answering my questions! And thank you for all the work you have done to contribute to the evolution of the quality of this instrument.
We can feel your passion for the handpan as we read your responses. As someone who has 2 or 3 of these Ayasa instruments at home, I have to say that you feel the passion when you play them too - to the point that I reshot my entire Essentials handpan course with a beautiful Kurd 10 Ayasa Ember Steel. I love you guys.
As a player it’s a real privilege to know people like you. You work hard, always wanting to hone your craft. You have always been attentive to details, quality, feedback and suggestions. In short, the friendship between me as a player and you as makers is such a treat for me. You know me - I want as many people as possible to discover this instrument, learn to play it, and have fun with it.
Thank you for the part you play in this!